EPSON EXCEED YOUR VISION
- JP
- EN
Article
Piezo method launchesa revolution
in printing
innovation
The continuous evolution
in technology
and societal contribution
Epson's proprietary
Micro Piezo inkjet technology
Epson's Micro Piezo printheads lie at the heart of all Epson inkjet printers. This unique technology has been the driving force behind the growth of Epson's printing solutions business.
Inkjet printing is accomplished by ejecting ultra-fine ink droplets directly onto media such as paper. Originally, the most common inkjet printing technology was thermal inkjet printing, which uses heat to eject ink droplets. Epson, however, opted to focus on piezoelectric technology and has continued to innovate the technology ever since.
Piezoelectric printheads eject ink mechanically rather than by heating. Piezoelectric elements that change shape when voltage is applied provide the mechanical force. Since they do not heat the ink, piezoelectric systems are compatible with a far wider variety of inks and far more durable than thermal systems. Piezoelectric printheads precisely and accurately control the deposition of ink droplets to deliver both outstanding image quality and high speeds.
Epson's first inkjet printer, the IP-130K (known as the SQ-2000 outside of Japan), launched in 1984. It was a piezoelectric system and was well received for business use. Epson's efforts to advance the piezoelectric printheads culminated in the development of proprietary Micro Piezo technology.
The path to their development was extremely steep and difficult, but Epson's R&D team overcame the many challenges and obstacles along the way.
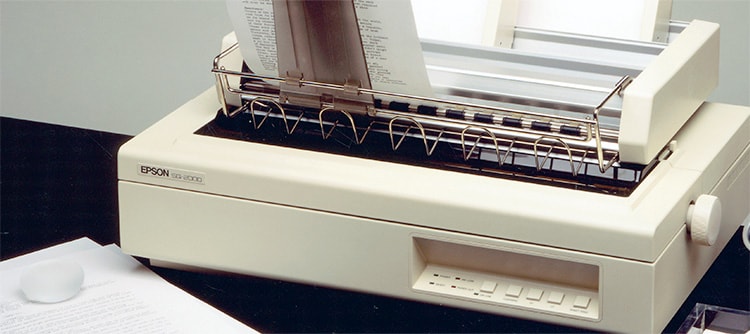
The first clear path to advent of
Micro Piezo technology
Around 1980, Epson's printing business was growing rapidly. Growth was driven by the TP-80, the company's first dot matrix printer (1979), and the MX-80, a printer for personal computers (1980).
However, the market landscape changed suddenly when a competitor released a laser printer in 1984. Dot-matrix printers could not match the quality and speed of these laser printers. Epson immediately recognized the threat to its business and reacted with a sense of urgency.
Within a few years, Epson would come across a chance clue that would enable it to overcome the threat. The clue involved piezoelectric technology.
In 1989, a European company proposed using piezo elements as actuators to drive the printheads in dot matrix printers. That is when a member of Epson's development team who was present at the meeting came up with the idea of applying piezoelectric elements to piezoelectric printers instead of dot matrix printers. This was the first major step toward the development of Epson's Micro Piezo technology.
Up to that point, Epson had been struggling with the high drive voltage and small changes in the shape of piezoelectric elements. But now Epson realized that these issues could be overcome by using multi-layered piezoelectric elements, which undergo greater changes in shape at lower voltages. With this discovery, Epson was able to establish technology that could compete against laser and thermal inkjet printers.
Ever-evolving Micro Piezo printheads
and their contribution to society
Major technical challenges had to be overcome to develop Micro Piezo technology.
First, the piezoelectric elements are made of a ceramic. The conventional way to produce the elements was to bake the ceramic like a brick, slice it thinly, and then polish it to the desired thickness. However, ceramic becomes very brittle when baked and the piezoelectric elements would crack or break when reduced below a certain thickness.
To overcome this technical issue, the development team came up with the idea of creating piezoelectric elements by stacking many thin layers of about 20 micrometers like a ceramic capacitor and dicing them into appropriate shapes to make an actuator. Thus, a thin-form piezo was achieved by creating the multi-layered structure before baking and stacking the piezoelectric elements in strips. This method was a game-changer in piezoelectric technology.
This is how Epson, through a lengthen process of trial and error, successfully developed the Micro Piezo printheads which paved the way to thinner piezoelectric elements and smaller printheads.
Micro Piezo printhead development started in 1990, and mass production was achieved by the end of 1992. In 1993, the Epson Stylus 800 monochrome inkjet printer became the first product equipped with as Micro Piezo printhead.
Micro Piezo technology continued to evolve. The next generation heads were dubbed ML Chips (multi-layer ceramic with hyper integrated piezo segments). Their piezoelectric elements were less susceptible to damage, which made the heads easier to produce in quantity. The were followed by TFP (thin film piezo) printheads, which had the thinnest piezoelectric elements possible, and finally by Precision Core printheads, which held the key to higher speed and image quality.
Micro Piezo printheads not only deliver superb performance, precision, speed, and image quality, but they also operate on low power, making them better for the environment. These features have enabled Micro Piezo printheads to quickly expand into the commercial, industrial, and office printing segments.
Epson's Micro Piezo printheads have the potential to evolve even further and meet an even wider range of needs. Printheads that are denser and more compact will enable higher image quality at a lower cost. Those with more nozzles will be able to print at even faster speeds. Advances like these will allow Epson to provide more reliable commercial and industrial inkjet printers.
Epson will continue to ceaselessly innovate and evolve Micro Piezo technology into the future.
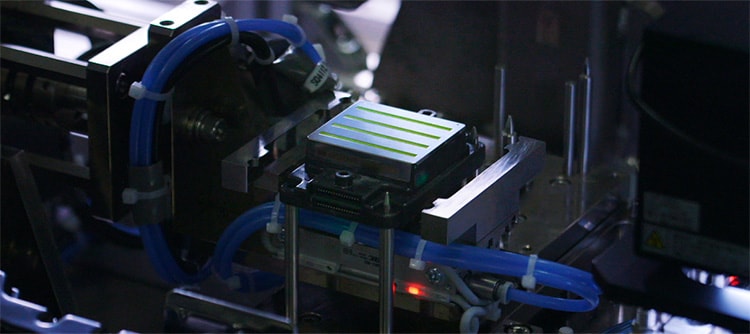